|
 |
|
HIP is a forming and densification process achieved through the application of heated high-pressure gas uniformly on all sides of an object. HIPping can virtually eliminate porosity, and is widely used to improve the properties and service life of a broad range of products and parts. It can be applied to both containerized powder shapes and preformed metal, ceramic or plastic components. Related functions include near net-shape forming, diffusion bonding of dissimilar materials, and the elimination of voids in castings. |
|
 |
|
 |
|
Prestressed wire wound vessel & Frame : Safest design |
Workzone diameter : 95mm - 254mm with graphite furnace. |
30,000psi and 2000¡É with graphite furnace(standard) |
Computer base control system Laboratory & Pilot |
|
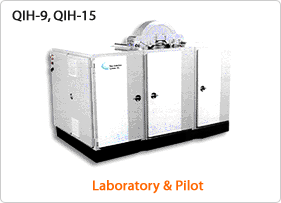 |
|
 |
|
|
Model
Number |
Work Zone Dimensions
(I.D x Height) |
System Dimensions |
Approximate
Total Weight |
FeCrAl |
Molybdenum |
Graphite |
uniform
Rapid
Cooling |
Subsytem Cabinet
Width Depth Height |
Vessel & Frame Assembly
Width Depth Height |
MIH-3 |
2.9 x 4.9"
75 x 125mm
|
4 x 5"
102 x 127mm |
3.75 x 5.9"
95 x 150mm |
Not
Available |
56" 48" 4"
1422mm 1219mm 1219mm |
Included in cabinet |
3,500 ibs.
1,588 kg |
QiH-9 |
6 x 12"
152 x 305mm |
6 x 12"
152 x 305mm |
6 x 12"
152 x 305mm |
Available |
85" 51" 61"
2160mm 1295mm 1550mm |
Included in cabinet |
4,560 ibs.
2,068 kg |
QIH-15 |
8 x 12"
203 x 305mm |
8 x 12"
203 x 305mm |
8 x 12"
203 x 305mm |
Not
Available |
95" 54" 73"
2413mm 1372mm 1854mm |
Included in cabinet |
4,841 ibs.
2,318 kg |
QIH-15L |
8 x 19.6"
203 x 500mm |
8 x 19.6"
203x 500mm |
8 x 19.6"
203x 500mm |
Not
Available |
55" " 95" " 53" "
1410mm 2415mm 1350mm |
52" 150" 84"
1321mm 3810mm 2134mm |
7,875 ibs.
3,580 kg |
QIH-21 |
9.9 x 30"
252 x 762mm |
9.9 x 30"
252 x 762mm |
9.9 x 30"
252 x 762mm |
Available |
Free-standing modules |
96" 156" 110"
2438mm 3962mm 2794mm |
13,400 ibs.
6,080 kg |
|
|
|
QIH-15L, QIH-21 cabinet includes cooling and electrical subsystems only. |
Press and compressor are separated from press module. |
|
 |
|
 |
|
Prestressed wire wound vessel & Frame : Safest design |
Workzone diameter : 226mm - 1600mm with graphite furnace |
Available also for temperatures up to 3000¡É under pressure and temperature up to 2000¡É under vacuum |
Reliable furnaces with short process cycle time |
|
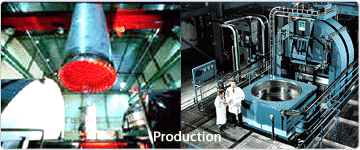 |
|
 |
|
User can select among several modular plug-in furnaces, depending on the temperature
and atmospheric requirements of the application : |
|
1. Iron- chromium-aluminum (FeCrAl) |
Iron-chromium-aluminum(FeCrAl) furnaces generate temperatures up to 1200¡É, and are |
capable of operating in a concentration of up to 20% oxygen in a balance of argon. |
Typical applications include oxide ceramics for the electronics industry. |
|
2. Molybdenum |
Molybdenum furnaces, with temperatures to 1450¡É, are suitable for applications |
requiring a clean environment, such as alloy metal densification. |
|
2. Graphite |
Graphite furnaces are designed for use in argon and nitrogen up to 2000¡É, and their high resistivity |
make them very well suited for vacuum operation, where low voltage is necessary. |
These furnaces are commonly used to strengthen and increase durability in non-oxide ceramic parts. |
|
 |
|
processing that powder pressure |
porosity remove of cast-iron ware |
composition of metal powder |
aerospace industry |
The HIP process heals internal cracks and porosity in sintered and cast parts. |
This improves the mechanical properties and reduces the scatter and thus allows greater freedom of design. |
|
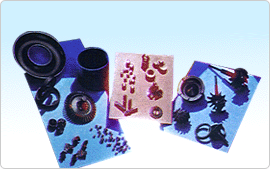 |
|
¡Ø If you need more information or catalogue, please give e-mail to us or visit web site of
¡Ø Avure Technologies AB, Avure Autoclave Systems, Inc. |
|